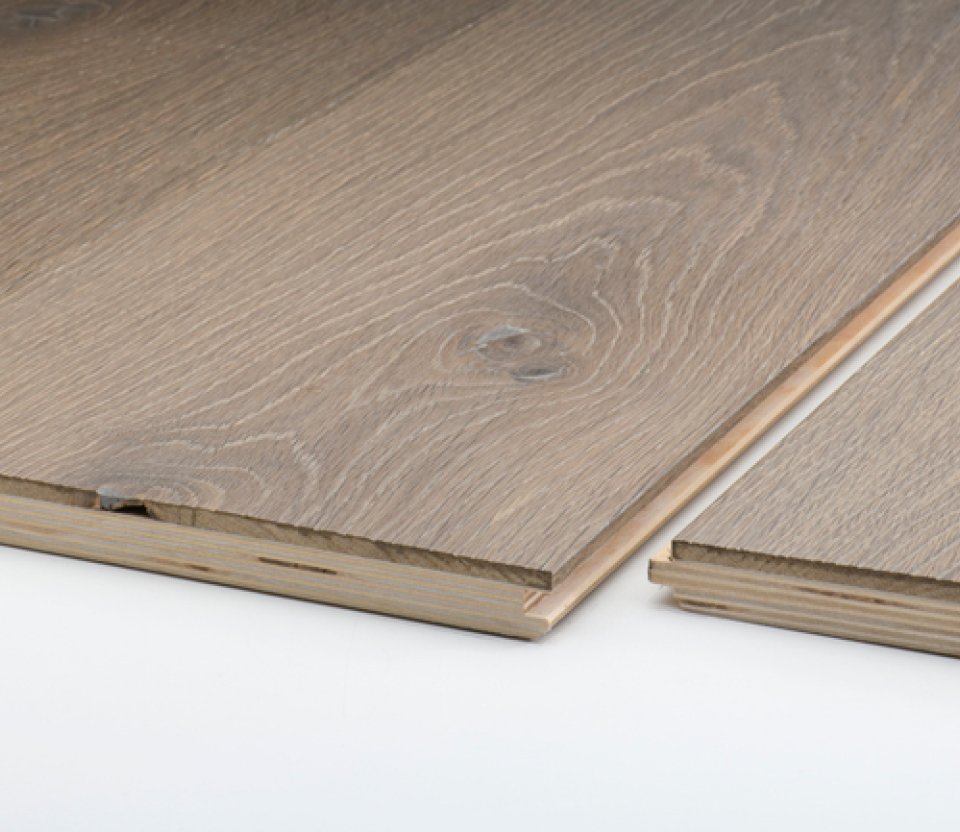
Featured FAQ's
What is engineered timber flooring?
FAQs
Browse our most frequently asked questions.
Samples
Where do you deliver samples?
We deliver samples nationwide in NZ. If you are located outside of NZ, please contact us to discuss your project before requesting samples
Do I need to pay for samples?
No - we supply samples delivered to your door completely free of charge (NZ only)
How many samples can I order?
There is currently a limit of 6 loose samples per order. If you require more than this please get in touch with our customer service team.
How long will my samples take to arrive?
We aim to dispatch all sample orders within 1 working day. If your sample order is going to take longer than 1 working day to dispatch you will be advised by email.
- Auckland area: 0-2 days
- North Island (excl Auckland): 1-3 days
- South Island: 1-4 days
- Other Countries: Please contact us
If you require your samples urgently please call us on 0508 35 66 77
Stock Availability
What does 'Availability: stocked' mean?
Stocked products are those which we endeavor to hold stock of at all times. However, due to unforeseen demand stock may not always be immediately available. If stock is not immediately available, it is likely that another batch is in production or being shipped.
WHAT DOES 'AVAILABILITY: CUSTOM ORDER' MEAN?
Custom Order products are those which are not stocked but can be ordered in for you. Custom orders will have lead times, usually between 12 and 20 weeks depending on the country of origin. For custom orders we require a 50% deposit before the product can be manufactured, with the balance payable before dispatch. Due to the nature of custom products we cannot accept returns unless they are faulty or defective.
WHAT DOES 'AVAILABILITY: DROP-SHIP' MEAN?
Drop-ship means that when you place an order, the product is sent direct from the supplier to you rather than being sent from our warehouse. Drop-ship usually applies to products like adhesives, moisture barriers, stains etc.
Can I reserve stock for my project?
Yes you can reserve stock. To do so we require a 50% deposit, as it means we no longer have the product available to sell to other customers. Stock can reserved for up to 3 months (or even longer by prior arrangement) in order to guarantee delivery as and when required. Alternatively we can secure the stock from the next available shipment – we do our best to keep our stocked ranges available at all times.
How far in advance should I reserve stock for my project?
It is recommended to lock in your stock 3-4 months before the product is to be required. This will help to ensure the product is available when you require it.
If you are looking to purchase a custom or special product (made to order and/or bought in specially for your project), it is a good idea to finalize your product selection up to 5 months before it is required, to allow for manufacturing time and shipping from overseas. The lead time required will vary between products depending on manufacturing processes and shipping origin.
What happens if the product I wanted is out of stock?
If you do not put stock on hold in advance, we cannot guarantee that the product will be available when you require it. We do our best to ensure all stocked products are available at all times - however sometimes due to high demand and/or shipping delays and other unforeseeable circumstances, stocked products may occasionally be unavailable. On occasion we are able to free up stock if another customer doesn't require their product until a later date and therefore can wait for the next shipment. There is often more stock arriving within a month or two. If we are unable to supply the product in your required timeframe we may suggest a similar alternative product.
Storage
Can you store my product until I require it?
Yes, we have warehouse space available for storing and delivering your order in manageable consignments. Storage fees may apply, please contact our customer care team to enquire.
Delivery
Where do you deliver?
We deliver our products nationwide in New Zealand. We can also ship product overseas. If you are not based in NZ and are interested in purchasing our product please make an enquiry.
What delivery options do you have available?
For sample orders, we delivery by courier. For product orders, we offer standard freight carrier and hi-ab deliveries to most areas in NZ. For more information please contact our customer service team.
How much will delivery cost?
For sample orders, delivery is free of charge. For product orders, delivery pricing is calculated using information such as the delivery type (freight truck or hiab), area you are located, and weight and volume of your order. For this reason we can't determine your exact delivery cost until your order is finalized
When will I receive my order?
Our standard delivery timeframes are as follows:
- Northland: 3-5 days (non-rural)
- Auckland: 1-2 days (non-rural)
- Auckland-Wellington: 3-5 days (non-rural)
- South Island: 5-7 days (non-rural)
- Rural addresses: Allow an additional 1-2 days
Damaged Goods / Product Issues
My product has arrived damaged - What should I do?
In the instance that your product arrives damaged please complete the process outlined below.
• Signed goods as damaged upon delivery
• Photograph the damaged goods on the same day
• Notify our Customer Care team
• Submit a Return Authority form (together with photos and order details) within 24 hours of receiving goods damaged in transit
For more information click here
I am not happy with my product - what should I do?
Read our article 'Buyer awareness - Natural timber products' to ensure what you are unhappy about is in fact a reasonable complaint and not something that is deemed acceptable in the industry.
If you believe your issue with your product is in fact reasonable, please hold off from installing the product and contact our customer care team to discuss.
My product seems to be faulty or defective - What should I do?
We stand by the quality of our products. If you have an issue with your product please hold off from installing the product and contact our customer care team to discuss.
Returns
Do you accept returns?
Yes, we accept returns of all products that are unopened and undamaged, in original condition of purchase - with the exception of clearance/end of line or indent/special order/custom made products.
To read our full returns policy click here
Do you charge for product returns ?
No - there are no fees for returning product. However should the product require shipping, the cost of return freight will be deducted from your credit
Can I drop off my returns to a Forte showroom?
No, we do not accept returns to our Showrooms. To ensure minimal staff handling and efficient processing, all returns must be delivered to our Warehouse.
Do I need to complete a Returns Authorisation form?
Yes, a Returns Authorisation form is required for all product returns. This ensures our staff know who returned the product and what job it relates to - which in turn enables us to process your credit in a timely manner
Trading Accounts
Can I open a trading account?
Yes - if you plan to purchase from Forté regularly, it may be convenient to apply for a trading account. Please note - Forté reserve the right to decline any request for a trading account, or decline a trading account application should it not meet our required criteria. Please contact us to enquire about opening an account
What are your account payment terms?
• First order to be paid up front in full
• Following orders due 20th of month following invoice date
Timber flooring basics
What is solid timber flooring?
What is engineered timber flooring?
What is laminate flooring?
The term laminate flooring often gets confused with engineered timber flooring, however the two are very different. Laminate is an entirely man-made product with a surface that imitates the look of timber, whereas engineered timber flooring has a real timber surface layer.
What does pre-finished mean?
What does unfinished mean?
General knowledge & FAQ's
What is the difference between herringbone and chevron?
Treatments, textures & finishes
What is a lacquer?
What is natural oil?
What is UV oil?
What is a reactive stain?
What is Sugi Ban?
Sugi Ban (also known as Shou Sugi Ban or Yakisugi) is a traditional Japanese method of wood preservation which involves charring the surface of wood with fire. Find out more
What does 'brushed' mean?
What does 'hand-scraped' mean?
What does 'rough sawn' mean?
What is smoked timber?
Edges, joints & profiles
What is a square edge?
What is a bevelled edge?
What is a micro-bevel?
Installation
When working to a achieve a specific floor height, what height should I allow for glue?
We recommend allowing an additional 2mm on top of the thickness of your floor for glue. E.g. Thickness of floor covering + 2mm allowance for glue = total floor height allowance
When working to a achieve a specific floor height, what height should I allow for underlay?
If you are floating your timber floor on an underlay you will need to allow for the thickness of the underlay you plan to use. E.g. Thickness of floor covering + allowance for underlay = total floor height allowance
Aftercare
How do I repair dents and scratches on my forte floor?
Small Surface Scratches - You could look using Osmo Maintenance Oil (Hardwax or Silkmatte finishes) or Bona HD Traffic Extra Mat Polyurethane (Lacquer Finishes and apply this with an artist brush over the scratch. This should disguise the white mark and seal in any exposed timber.
Medium scratches or small dents - You could look at wax filling these. Briwax Filler Sticks are what we recommend. Just look for the shades that are a close match to your floor.
Major Dents and Scratches - Major damage will require a timber repair specialist or removal of the damaged plank and installation of a new one. This should only be carried out by a professional floor installer.
What is covered and not covered on my forte floor?
Please refer to our Structural Warranty – Timber Flooring &
Wall Panelling
How do I care for my forte floor?
LACQUER FINISHES
1. Clean the floor from sand, dust and other debris with a vacuum cleaner with a soft bristle head. To prevent damage to the lacquer finish of your floor, ensure the wheels of the vacuum are clean and freewheeling.
2. Clean with a Bona® Spray Mop and microfiber pad using Bona® Wood Floor Cleaner solution. Mop along the length of the board. Wipe the surface using a microfiber mop until the floor is nearly dry. Alternatively, use a Kärcher FC5 Floor Cleaner.
HARDWAX OIL & SILKMATTE FINISHES
1. Clean the floor from sand, dust and other debris with a vacuum cleaner with a soft bristle head. To prevent damage to the lacquer finish of your floor, ensure the wheels of the vacuum are clean and freewheeling.
2. Clean with a microfiber mop using the Osmo wash and care. Alternatively, use a Kärcher FC5 Floor Cleaner.
For more information, refer to our Forte Care and Maintenance Guide
How do I protect and maintain my forte floor?
For more information regarding periodic maintenance, please refer to our Flooring Care and Maintenance Guide.
Decking general knowledge
What is solid timber decking?
What is composite decking?
What is RMC decking?
What is WPC decking?
What is PVC decking?
About
What is Millboard decking?
Usage & applications
Can I install Millboard decking around swimming pools and hot tubs?
In all parts of the world Millboard is used to surround swimming pools and hot tubs in homes, leisure parks, seaside resorts, and hotels.
As with any material surrounding a pool, deposits in the water (from chemicals in the pool water, unintentional spills, suntan lotions, creams etc) can get splashed onto the boards and leave stains, which can be difficult to remove if left to build up over time.
A well-considered pool design, good installation, and a regular cleaning regime will all help to minimise the likelihood of staining and colour damage to the boards. Millboard should not be installed below the waterline, or on the vertical area just above the waterline where it is constantly wet from wave action.
Ideally you should frame your pool edge with stone, concrete, or tile (you may install a drainage grill), then install your Millboard terrace from this frame.
Where Millboard edgings are used to frame the pool edge, regular maintenance is important, as the pool edge is the area of the deck most subjected to water evaporation and deposit build-up. We also recommend painting the underside of any overhanging Millboard edgings with our Touch-Up Paint; because Millboard is a moulded product the underside of boards/edgings are not coloured. This is purely for aesthetic purposes as the underside of boards may be seen from the waterline. Millboard is non-porous so does not need sealing.
Just as your vehicle needs regular cleaning to remove road traffic particles and other deposits, your Millboard terrace should also be cleaned regularly. We recommend washing the boards with warm soapy water and scrubbing with a stiff brush. Stubborn deposits that have been left to build up on the deck may require a specific cleaning solution (as outlined in our Product Care Guide).
Millboard shall be under no liability in any respect of any defect arising from incorrect installation; willful damage or abuse; negligence by the buyer or any third party; surface deposits; chemical staining; weathering. For full details please refer to the relevant
Millboard Limited Structural Warranty on our website - https://www.millboard.com/engb/ limited-structural-warranty-registration.
Where can Millboard be used?
Does Millboard tolerate snow and ice?
Can I use a fire pit or brazier on my Millboard deck?
Can I use a gas or infrared heater on my Millboard deck?
Performance
Does Millboard expand and contract?
Does Millboard decking fade?
Does Millboard decking get hot in the sun?
Is Millboard slip-resistant?
Does Millboard decking stain?
Does Millboard decking scratch?
Does Millboard have colour variation throughout the boards?
How long does Millboard last?
Care & maintenance
Can I paint or stain Millboard?
Do I need to seal Millboard?
Does Millboard require maintenance?
How do I clean my Millboard deck?
Environment
Is Millboard decking Sustainable?
Millboard decking boards are ideal for use as part of a sustainable design strategy. Their extended design life dramatically reduces the need for repair and replacement.
Millboard as a company is focused on continued sustainability and have become the first premium outdoor flooring company in the world to have their carbon footprint independently verified. The embodied carbon of Millboard decking has been verified as 1.31kg / CO2e per m2.
Millboard is an ISO 14001 certified company, complying with international environmental management practices. They are the only carbon-verified premium timber-free outdoor flooring material in the entire world.
For more information on Millboard sustainability refer to our article on Millboard Decking Sustainability.
Pricing
How does the cost of Millboard compare to other types of decking?
The subframe material and installation labour costs of Millboard are comparable to traditional decking. Upon purchasing, Millboard may appear more expensive than timber decking. However, if you take into account its greater durability, increased lifespan and reduced maintenance requirement, the life cycle cost of Millboard is considerably less than that of timber decking. For more information refer to our article How does the cost of Millboard compare to other types of decking.
Technical
What are Millboard's dimensional tolerances?
The manufacturing tolerances for Millboard are; Width: ± 3mm. Length: ± 5mm. Thickness: ± 2mm.
There will always be a slight variance in the board’s dimensions due to the fact that Millboard planks are moulded from natural oak, and due to the pressure of the moulding process. Despite this, Millboard calibrate the boards to maintain as consistent a profile as possible.
The dimensions of the Weathered Oak style may vary more between moulds due to the fact that they are moulded from timeworn oak with minimal changes to the dimensions. When working with the boards, packers can be used to create a flush finish between two boards.
Installation
What fixings should be used to install Millboard?
How do I cut Millboard decking?
Can I use an impact driver to install Millboard?
What joist spacing is required for Millboard Decking?
What Expansion Gaps are required for Millboard decking?
Millboard recommend allowing a minimum of 4mm between the lengths of the boards and a 1mm gap between the ends of board. A 10mm gap should be left between the boards and any solid surface to aid drainage.
The recommended 4mm gap between Millboard lengths is very minimal considering the width of the planks (176mm for -200mm wide). In comparison, a 6-8mm gap between lengths is recommended for most solid timber decking planks between 130-140mm wide, and a 5mm gap between lengths is commonly recommended for most traditional composite decking between 136-140mm wide. With Millboard you can have wider boards with narrower gaps - a better look overall!
Can I use a standard board as an edging piece?
Yes you can, where the edge is merely aesthetic, such as a balcony edge, if this is your preferred finishing option. However, where the edge is likely to sustain impact, such as a step, we do not recommend using a standard board. Our edging boards have been specifically designed with high impact in mind and as such have a thicker Lastane® surface to withstand the knocks and scrapes associated with step edges and other associated applications.
Can I bend Millboard?
Can you recommend an installer for Millboard?
Aftercare
How to repair dents and scratches on my Millboard deck?
Small Surface Scratches - To help disguise scratches, this can be touched up using the Millboard touch-up paint. Apply this with an artist brush keeping the painted area to a minimum so it doesn’t stand out when the paint dries.
Dents and Gouges - Carefully repair the holes with a PU based filler/sealant such as grey SikaFlex 221. Carefully repair the holes with a PU based filler/sealant such as grey SikaFlex 221.
It is best he put a small amount into the hole and then immediately wipes off all the excess from the surrounding surface. Then after the sealant/adhesive is dry, touch up paint the repair with Millboard touch-up paint using an artist’s paintbrush.
What is covered and not covered on my Millboard deck?
Please refer to Millboard’s Structural Warranty.
How do I care for my Millboard deck?
We recommend cleaning your deck twice a year or as required. As an exterior product, Millboard will benefit from this periodic clean to remove any accumulated dust or dirt residue.
1. Wet the area with water 10-15 minutes before applying any cleaning solution.
2. Spread foaming cleaner onto the Millboard deck to help lift dirt out of the grain. Our preferred regular cleaner for Millboard is Wet & Forget Double Bubble House Wash.
3. Using a hard bristle brush or broom, scrub the surface of the Millboard to loosen any dust and dirt. We recommend the Browns Superior Deck Scrub.
4. Thoroughly rinse off the house wash solution using a hose. Ensure all the solution is washed off and avoid letting it dry on the surface.
How do I protect and maintain my Millboard deck?
For more information regarding periodic maintenance, please refer to our Millboard Care Guide.
Warranty
Does Millboard decking have a warranty?
Samples & purchasing
How to calculate how much Millboard I need?
Troubleshooting & repairs
What happens if a Millboard plank gets damaged?
For minor repairs, Millboard produce touch-up paint specific to each decking colour they produce - this can be applied to smaller surface scratches as a means of repair. If a board is seriously damaged you may prefer to removed it and replace it with a new board. For more information on how this can be done refer to our article titled How to uplift & re-fix Millboard decking boards.
Why is Millboard edging thicker than Millboard planks?
Millboard have deliberately designed the Bullnose and Square edging to be 1mm higher than the standard plank due to areas such as steps and edging sustaining higher wear than regular planks. On these edging profiles, the Lastane layer is significantly thicker and is therefore designed to handle the additional wear required as well as provide extra slip resistance. The additional height also ensures no wear will occur on the edge of the adjacent board as the board edge is ‘shielded’ by the edging that sits proud.
Why are gaps appearing in my Millboard deck?
Why is water sitting on the surface on my Millboard deck?
Walls & Ceilings basics
What is engineered timber wall panelling?
Engineered timber wall panelling consists of a solid timber veneer adhered to a backing of ply, pine or hevea. It is designed to have superior stability over solid timber wall panelling but gives the appearance of a solid timber panelling when installed.
What is a lamella?
A lamella is a thin plank or sheet of solid timber, much like a wood veneer only thicker. Lamella thickness can range from 2.5-10mm, whereas veneers are usually less than 2.5mm thick.